Lead Time: What Is It and How to Calculate It + Benefits
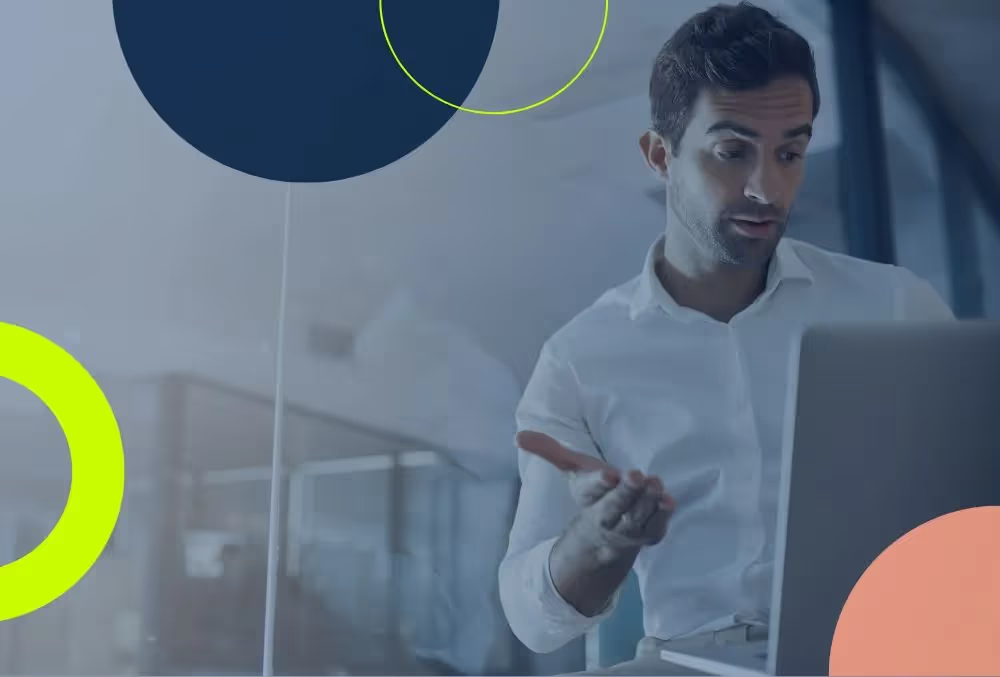
Lead time refers to the time between the start and end of a process. Businesses can utilize lead time in different areas such as inventory management, manufacturing, and project management. It is a very useful way of keeping everything in control in terms of running a business.
Shortening lead time can enhance operational efficiency and boost productivity, leading to higher output and revenue. Conversely, extended lead times can adversely impact sales and the manufacturing workflow.
What is Lead Time?
Lead time refers to the period required to complete a process from its initiation to its conclusion. Specifically, in retail, 'lead times' often encompass:
- The time taken to stock inventory in a store or warehouse, starting from when it's ordered from a supplier until it's ready for sale to customers.
- The duration it takes for a customer's order to be delivered, from the moment of purchase in-store or online to the point of delivery at the customer's chosen location.
Understanding and calculating these lead times is crucial for retailers to manage delays effectively. Many retailers factor in a slight buffer in their lead times, recognizing that unexpected issues can arise throughout the supply chain. Retail recruiters can assist by helping retailers find the right talent to keep things running smoothly.
To explain lead time better, let’s talk it over an example:
Imagine you run a clothing company that gets its products from a third-party retailer. To keep your stocks in control, you need to use lead time in inventory management. To calculate your lead time, you need two different numbers. The first number is the number of days it will take you to request an order from your retailer. The second number is the number of days that it will take your retailer to deliver your products. After you get these two numbers, you sum them up to calculate your lead time.
How to Calculate Lead Time?
Continuing with the earlier example, let’s give hypothetical numbers to calculate lead time in inventory management for your clothing business:
The number of days it will take you to place an order (procurement): 2 days
The number of days it will take the retailer to deliver your order: 8 days
Summing up these two numbers shows you your lead time: 10 Days
The lead time for this appeal company is 10 days. This means in the next few days you need to manage your inventory according to that lead time, or else your business might face a stock problem.
The Formula of Lead Time:
%2520%252B%2520Shipping%2520Time.png)
Lead Time vs Delivery Time - What is the Difference?
So far, lead time and delivery time might have looked like the same thing, but they are not. They have a huge difference. Lead time includes all the things that might prolong that process while delivery times only consider the time spent during delivery.
So once again going back to the earlier example of lead time in inventory management, two different values are summed up to calculate lead time. One of these numbers is the days you need to place an order.
Delivery time, on the other hand, only includes the time it takes a retailer to deliver your product, so it does not include the days that pass on your company’s part.
In the end, when calculating the lead time, one should consider all the things that can affect the process to reach the right results. If not, it might have harmful consequences for their business.
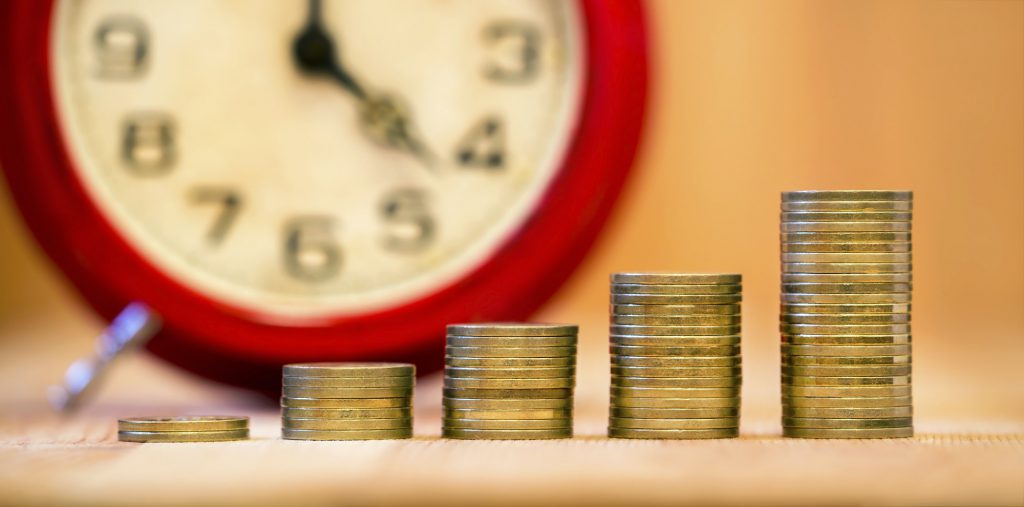
Why is the Lead Time Important?
Lead time is a critical aspect of inventory management, and businesses need to thoroughly understand and effectively manage it. Neglecting lead time control can trigger significant ripple effects, leading to customer delays.
The lead time might seem like an extremely easy math question on the surface. The benefits of lead time might not be visible the first time you use it. The second or third times might not differ. However, the fourth time, it might be exactly what you need to keep your business alive. If lead times begin to spiral, a detrimental cycle can ensue, with lead times worsening as supply chain bottlenecks increase the demand for more units.
Ineffective lead time management can lead to stock shortages and unfulfilled customer orders. Poor order management can significantly harm a business's reputation, risking loss of customers to competitors. Therefore, it's vital to take all possible measures to maintain control over lead times.
Lead time is almost like a safety net for your company in certain processes. That safety might not serve a purpose if nothing is wrong with the processes. Yet, if you properly utilize that safety net in your time of need, your business can avoid many potential disasters.
What are the Impacts of Long Lead Time?
Managing and reducing lead times is essential for maintaining customer satisfaction, efficient inventory management, and overall business agility. Long lead times can have several significant impacts on a business:
Out of Stock or Unfulfilled Orders
When suppliers fail to deliver purchase orders on time or in correct quantities, it disrupts a business's operations significantly. This situation forces businesses to rely solely on their current stock to meet orders. If this stock is inadequate for customer needs until new inventory arrives, customers may experience delays or incomplete orders.
Negative Customer Experience
The length of lead time plays a crucial role in shaping customer experience. With the abundance of options available today, consumers can easily switch to other retailers after negative experiences. Delays in orders or inability to find desired products often drive them to look for alternatives.
High Storage Costs & Cash Flow Issues
Consistently extended lead times can inflate storage costs, as businesses might need to maintain larger inventory levels to meet demand. This can lead to increased product prices and make the business less agile while increased inventory levels due to long lead times can result in more capital being tied up in stock, affecting the liquidity and cash flow of the business.
How to Manage Lead Time Efficiently?
Even while you can't control every lead time, there are strategies you can use to better manage lead times across your supply chain. Here are some pointers for better lead time management.
Have Multiple Suppliers
Maintaining relationships with backup suppliers ensures preparedness for emergencies or stockouts caused by primary supplier issues. If current suppliers are consistently causing delays, finding reliable alternatives that can meet deadlines is crucial.
Inventory Management Software
Utilizing tools like Fabrikatör’s automated inventory management software can simplify supply chain management. This software offers features for managing multi-store inventories, smart demand planning, and real-time insights into sales, profitability, and costs.
Choose Air Freight Over Ocean Freight
In urgent situations, such as before major sales events, opting for air freight, despite its higher cost compared to ocean freight, can significantly reduce lead times. Fabrikatör’s freight planner allows you to manage your optimal lead times and lower your costs.
Adopting an Inventory and Order Fulfillment Platform
Efficient inventory management and order fulfillment are key to reducing lead times. While in-house management is possible, outsourcing to experts like third-party fulfillment providers can be beneficial. Platforms like ShipHero offer full-stack fulfillment and warehouse management systems.
In conclusion, lead time is a term used frequently in business to indicate how long it takes to process an order, produce a commodity, deliver a good, or carry out a combination of these tasks. Shorter lead times may result in fewer finished products being on hand, more cost-effective procedures, and generally happy customers for businesses.
Manage Inventory Like a Pro with Fabrikatör!
Fabrikatör stands out as a cutting-edge solution tailored for Direct-to-Consumer (DTC) and ecommerce companies, offering a comprehensive suite of tools designed to optimize and streamline their supply chain processes. Key among its offerings is the ability to significantly reduce lead times, which is crucial in the fast-paced DTC market. By integrating advanced analytics and automation, Fabrikatör helps businesses in forecasting demand more accurately, managing inventory efficiently, and coordinating with suppliers seamlessly.
Additionally, Fabrikatör's platform enhances transparency and communication across the supply chain, allowing DTC companies to make more informed decisions, adapt to market changes swiftly, and maintain a competitive edge. In essence, Fabrikatör is not just a tool but a strategic partner for DTC companies looking to scale efficiently while maintaining high customer satisfaction. Why don't you start your free trial and see it yourself?