How to Improve the Order Fulfillment Process: 5 Tips
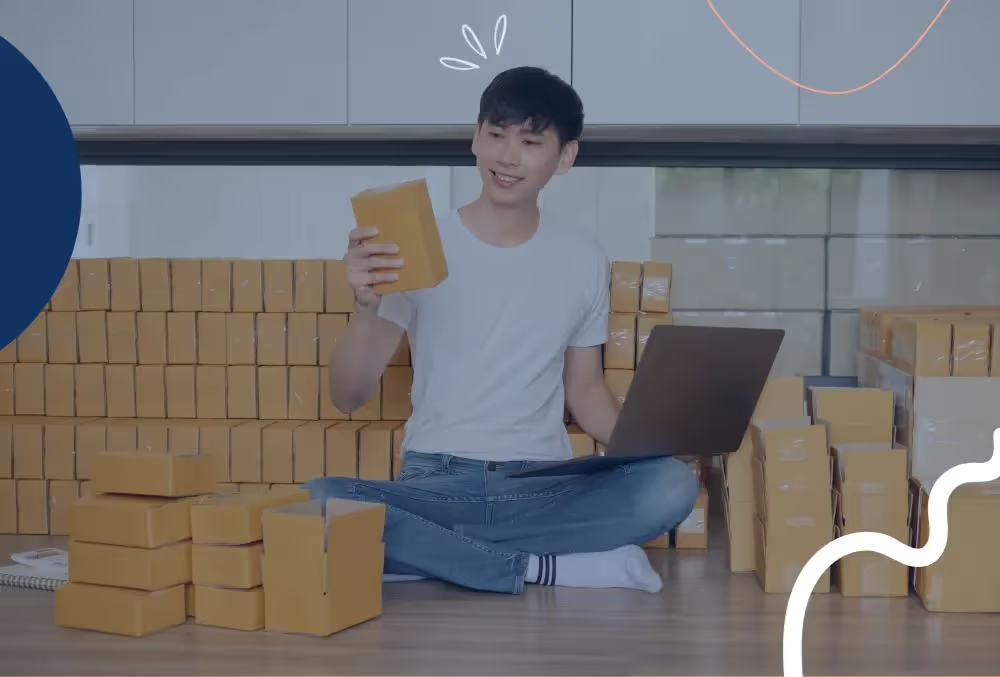
In-house fulfillment means fulfilling orders all on your own: all of your customer orders are processed, picked, packed, and shipped under your roof.
What is in-house fulfillment?
Order fulfillment is an operational process trusted by companies that sell products directly to customers. It is a process that encompasses everything from receiving products from suppliers or factories to selecting, packing, and sending orders to end customers.

In this case, if we talk about in-house fulfillment, it is because all customer orders are processed, selected, packaged, and shipped under the same company.
This means that the company is responsible for handling every phase of the order fulfillment process, including receiving and storing inventory.
Order fulfillment processes can be handled in-house or outsourced through a third-party logistics warehouse (3PL).
Differences between in-house fulfillment and 3PLs
With the internal fulfillment strategy, a business needs to have enough physical space to store product inventory and storage capacity for packaging materials, as well as to pack orders and prepare them for shipment.
The other choice is to outsource the order fulfillment process to a 3PL provider.
Choosing this option means the business will be relying on a third party to handle every phase of the fulfillment process. That means, inventory is received by the company and stored in the 3PL warehouse, and then orders are picked, packed, and shipped from this location.
With a 3PL warehouse, there are no direct costs. Instead, the cost is typically rolled into what’s called a per-unit fee.
Other benefits include:
Save money
Cutting costs is one of the most attractive reasons to opt for a 3PL. Instead of investing in inventory storage facilities, a 3PL shares these costs, labor, and transportation among multiple customers.
Optimize time
A 3PL fully assumes the responsibilities of taking care of an inventory, giving the company the time to focus on the business and optimize results.
Global reach
This allows operating in other countries, if this is what the company wants, it must be considered that it requires extensive knowledge of other markets, foreign laws, commercial relationships and entails a long list of new challenges. When working with a 3PL, you don't have to deal with the worry of monitoring warehouses and personnel from a distance.
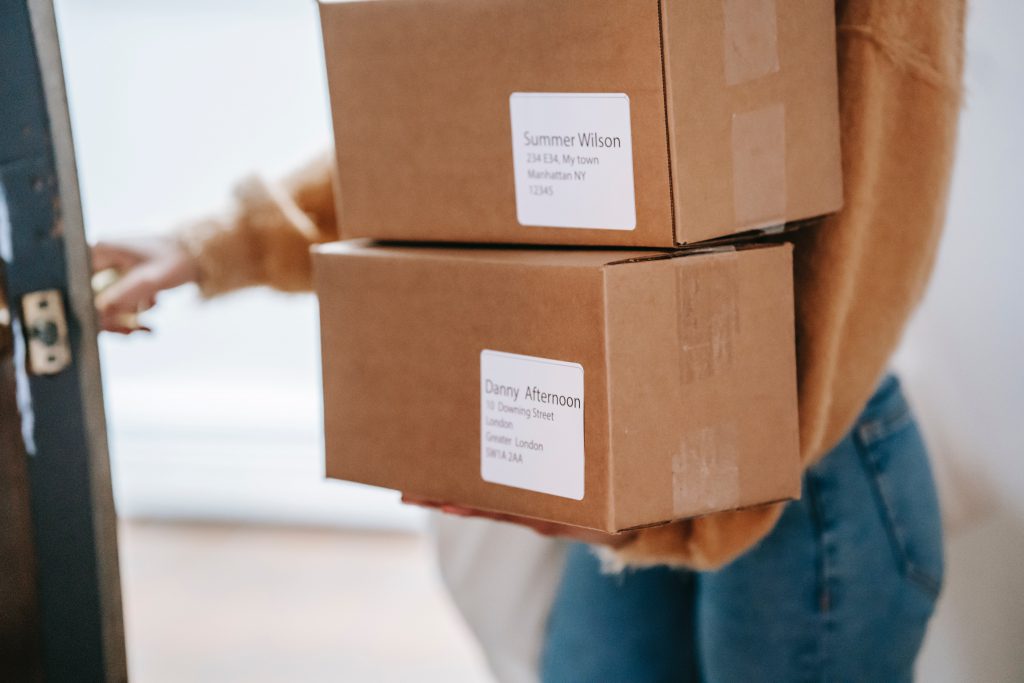
5 Tips to Improve Your In-house Fulfillment
Start Using Barcodes, Now!
Barcodes can be used in any warehouse, industry, or trade to identify any product regardless of its characteristics. Its use allows an agile flow of products as it is easier to record the entries and exits of inventories. This significantly reduces the time spent on the entire production chain and human errors, and therefore, logistics services and all those related to inventory, storage, transportation, and sale of items are improved.
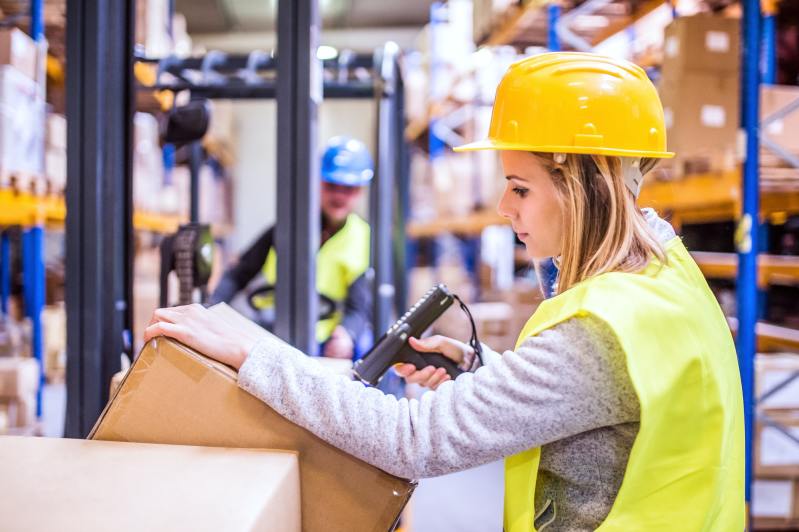
Previously, more bulky devices were used that were placed at specific points for merchandise tracking and inventory control. Today new tools and applications can analyze more data, faster and more accurately, helping to improve operational efficiency.
Among the new tools are portable barcode scanners, their use in shops makes the service faster and more efficient at the time of price inquiries and sales.
The structure of the barcode, being an international standard, is also useful in customs, for the import and export of products, since they are used to reduce the time spent passing through customs and streamline procedures by being able to review and inventory, at the same time that their international registration is verified that guarantees their passage through customs.
Finally, one of its most important benefits is reflected in the warehouses to keep inventory control. With a barcode reader tailored to their needs, they can track inventories in an automated way.
Each time a sale or item is received, the products in inventory will be discounted or increased, and at the end of the day, they can count on an accurate report of the products without the need for exhausting manual counts.
Organize Your Storage Space
The first key element that is often the source of poor organization is the warehouse design. It is important to focus first on consistent organization so that the warehouse will reach its maximum profitability.
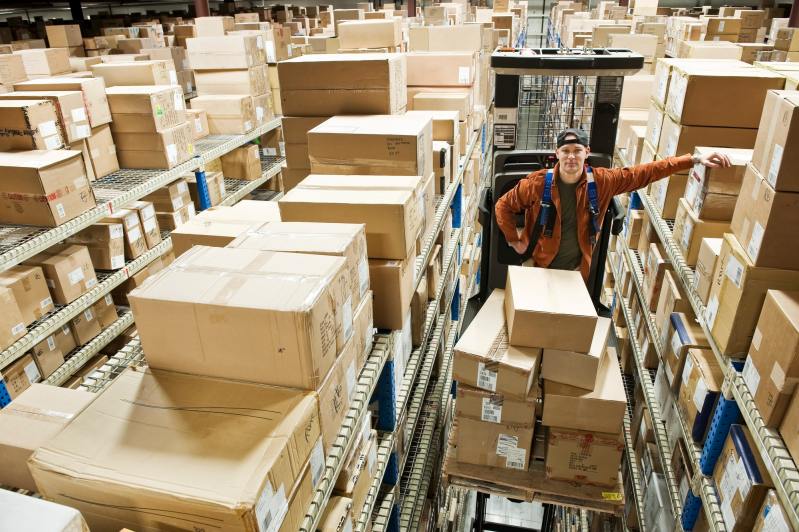
Thus, it is best to choose a storage system that is as efficient as possible and that adjusts to the type of goods that the company stores and also consider that a company can choose one or the other according to the distribution of spaces. There are different systems such as ordered, free hole, or according to input and output flows.
On the other hand, technology is constantly advancing and evolving, which is why it is possible to automate some of the processes that are more expensive on a day-to-day basis.
Use a Warehouse Management Software
An inventory management software is a computer program that allows companies to keep exhaustive control of each product or raw material. Thus, there is a record in the system every time there is any movement.
These software allow a detailed record of the inputs and outputs of the product, and a record of the quantities that exist, as well as their access and distribution.
Thanks to an inventory control system, the online store is connected to the warehouse, which allows optimizing processes, maximizing control and efficiency, as well as reducing errors.
Having all this control not only guarantees greater profitability but is also key for customers to get a good impression.
Shopify, for example, is great for eCommerce stores, but it is not built with warehouse control and inventory management at its core. Visit skusavy if you need extra help with tasks like:
- Automate inventory purchases based on sales volume
- Track inventory locations across multiple warehouses
- Enable picking-packing-shipping coordination
- Provide detailed inventory reports and action items
Keep Dedicated Fulfillment Space
In warehouses, the maxim must be order and cleanliness as it is essential. As well as a series of norms and guidelines to enforce or comply with this order. This is important because a disorganized and disorganized warehouse implies that the process will not be productive or add value.
Likewise, it is important to have a specific space for this type of activity in warehouses, special emphasis should be placed on preparation protocols, zoning preparations by employees so that the operator collects several orders at the same time, as well as that the merchandise comes to the operator. And in this same sense, distribute and air the products to the departure beaches. In this sense, each company or business will have its different nuances that will improve productivity.
To achieve an increase in productivity, the operations to be deployed must be analyzed, in each case, to help reduce preparation times.
Have a Shipment Policy in Place
Shipping policies are a set of rules and guidelines that describe how the shipping process of the products purchased will be carried out. These policies must appear on the marketplace or purchase page and must be easily accessible. In this way, the customer will be able to know what to expect and what not once he has completed his purchase.
Shipping policies are important because they provide confidence to the buyer (they provide specific information on how the shipment and delivery of their order will be managed) and constitute a legal framework of reference regarding the purchase made. In this way, they provide security to the purchase process and, in addition, allow the customer to know when and under what conditions they will receive their order.