What is Fixed Cost & How to Reduce Them?
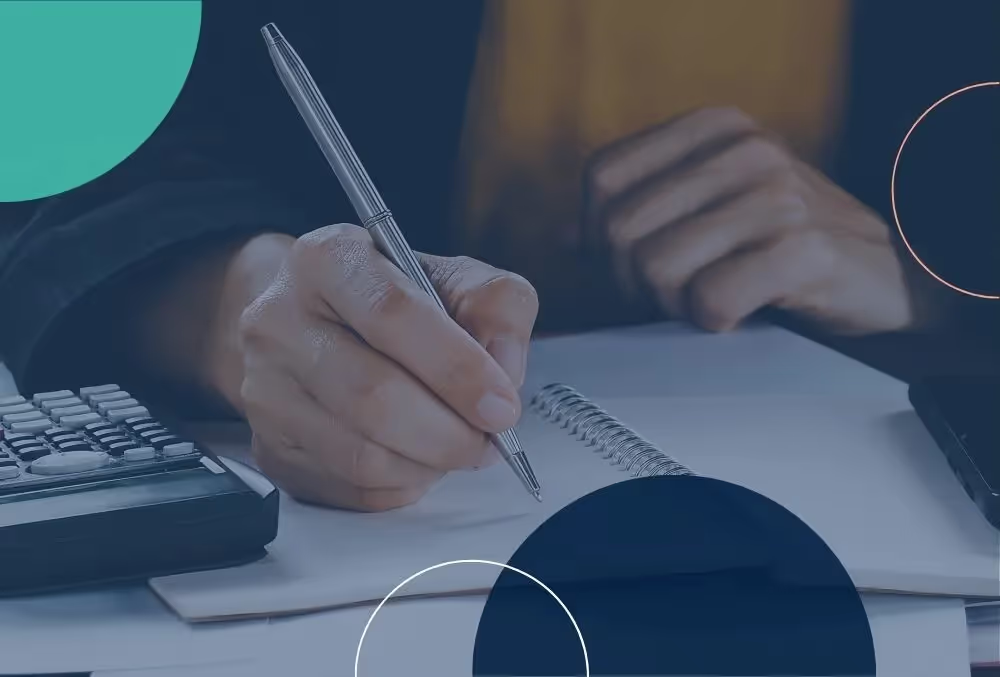
Manufacturing businesses should have regular expenses to run their operations. Business costs are divided into certain categories in order to better understand the nature of the cost and make required improvements to reduce them. Based on the nature and/or the function; cost are divided into certain group to better measurement. In general, the costs are determined in two major groups: fixed costs and variable costs. In this article, we will explain the fixed cost with some examples.
What is Fixed Cost?
Fixed cost is a type of cost in a production, sales and/or service businesses that does not depend on the quantity of product or service that created/provided. Fixed costs are the expenditures that the business should makes on a regular basis, regardless of any manufacturing activity. The fixed cost is the total expenses the business should make, even if it doesn't produce or sell anything.
What is Fixed Cost with Example?
The best examples of fixed costs are rent expenses and salaries paid to employees. Let's say you rent a shop and have a contract with an employee to work here. As a business owner you start paying for rent and salary are fixed and you'll need to pay them at the end of the month. Even if you do not start the manufacturing or sale operations you'll have to pay these two expenses at the agreed price. These costs are not in any way related to the amount of production you make. Even if your business does not produce at all in the first month, these costs will come out of your pocket.
How to Reduce Fixed Costs?
Unlike other costs, fixed costs are visible and easily countable costs. For example, an electricity bill is approximately the same when there is no special case. The salaries paid to employees will also be the same in the following month, if there is no change in the number of employees compared to the previous month. So, it is quite easy to calculate fixed costs as they are naturally countable. Reducing fixed costs on the other hand is a process requiring managers to make fine calculations.
Reducing the fixed costs process should be started by first calculating the efficiency of each cost item. Calculations as to which costs can be eliminated, reduced or replaced with a less expensive equivalent are the processes that the manager can manage with the experience s/he has gained to date. As an example, we can think of light bulbs used for lighting. If we use bulbs with high amperage value, then our bills will be high. However, the led bulbs, which are the equivalent of these bulbs, will both work longer and require less electricity. It is obvious that if a business using 50 bulbs replaces these bulbs with led bulbs, there will be a noticeable change in the electricity bill, ie the total fixed cost.
What is the Difference Between Fixed and Variable Costs?
Fixed costs are the costs that a business should spend on a regular basis to run its operations. Fixed costs have nothing to do with the production or sales activities in that entity. However, variable costs (also known as material costs) are directly related to production or sales. If you run a textile workshop, the rent of your shop and the salary you pay your employee are regular and clear. Even if you do not make production, you have to make these payments. So we can call these costs as fixed costs. However, the variable cost of top fabric depends directly on your production. If you don't make production, you can't spend these materials. In this case, your top fabric cost, which is a variable cost item, does not occur.